Wire at Every Stop
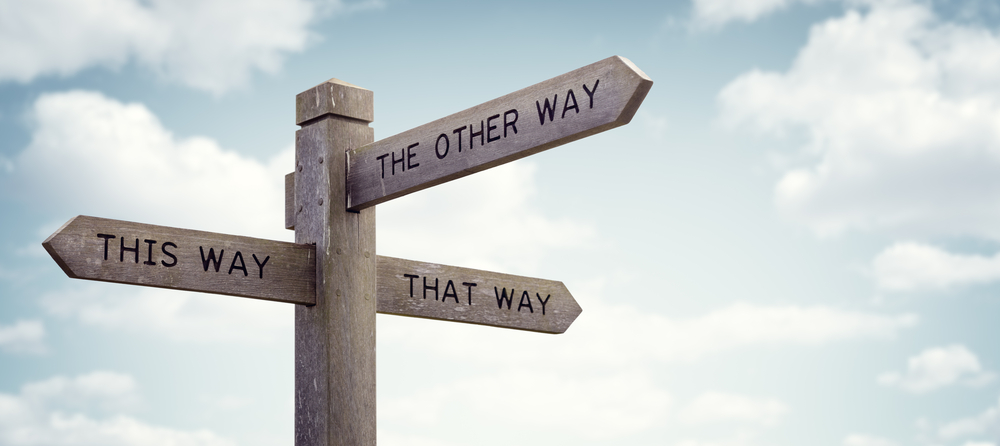
Our executive leaders, Radcliff Wire President Charlie Radcliff and General Manager Ryan Cei, hit the road last quarter to meet with customers. After visiting three Michigan companies in succession, they discovered interesting, previously unknown interrelationships among them.
Company One
At their first stop, Radcliff and Cei saw Radcliff’s wire being formed into a flexible coiled tube, which was subsequently jacketed by two layers of flexible plastic coating (substrate). This is typically applied to protect welding wire as it’s fed from the stem of welding wire to a robotic welding machine, to the point where the welding takes place. This flexible, coiled wire resembles a giant coated spring, and it’s used in lengths up to 100 feet for robotic welding.
Company Two
At the second company, Radcliff and Cei watched a conveyor belt manufacturer make staples for conveyor belts using Radcliff’s wire. They were delighted to note that the company used multiple robotic welding processes that employed the same flexible, coiled wire they witnessed being manufactured at company one.
Company Three
The third company they visited revealed another interconnection. This spring manufacturer uses several types of Radcliff wire to produce automotive springs and wire forms, but also has a stamping operation that uses conveyor belts to move scrap metal to their recycling area. Having just learned that company two makes 90% of the staples used to hinge conveyor belts in North America, it’s highly likely the staples in these conveyor belts were produced by the second company they visited.
To summarize, company one used our wire to produce the coated, flexible wire used in the welding machine that helped produce the staples for conveyor belts at company two, who then most likely sold those to the manufacturer of the conveyor belts used at company three.
These relationships demonstrate just how interdependent the wire industry is, and it highlights the domino effect of producing a high quality product. You never know just where it will end up!
Our executive leaders plan to visit more customers throughout 2024, and we can’t wait to see what those visits reveal.
Contact Us for wire that goes the distance.
Recent News
Free Programs Facilitate Funding for Manufacturers. Are You Missing Out?
Manufacturing companies in Connecticut have access to an impressive array of free resources designed to bolster their growth and improve Read More
Beryllium Copper: Wired for Defense
You don’t need a course in metallurgy to know that the addition of beryllium is what distinguishes beryllium copper wire Read More
The Wires Inside the Electric Vehicle Evolution
In the manufacture of electric vehicles (EVs), the choice of wire materials is instrumental in ensuring efficiency, safety, and performance. Read More
Triangle Shaped Wire: Some Food for Thought
It’s by design that some of America’s favorite foods, like pizza, nachos, and ice cream cones are served in Read More